Introduction
Since my Celestron 8″ is permanently embedded in my observatory until replaced, I need a scope I can easily load up in the truck and take places. Lately I’ve been reading Albert Highe’s Engineering, Design, and Construction of Portable Newtonian Telescopes, so I’m using his ultralight telescope design as a guide for the 16″.

Optical Tube Assembly
Originally I posted on Cloudy Nights for a 16″ mirror blank that I could grind myself expecting to spend about $500 for a good Pyrex blank. I got lots of responses, some much below $500 (for example one person offered a glass blank that needed to be edge ground for $145!) I was offered a 16″ F/4.5 Meade Starfinder mirror so for my budget, I was able to skip the laborious grinding of the mirror, and start building structure right away. So I went for it! Images below:


The seller’s comments were:
The shots don’t show exactly what the eyes can see. On the primary there are several minor sleeks that don’t show up as well as number of places where the aluminum coating is starting to show its age. The secondary also has a small defect in the coating at one end. If you look at the photos real close you can see the defects. They will appear as slightly “lighter” spots within the reflected image. None of these appears to be into the glass itself, just the coating so if you intend to recoat them (certainly if you refigure) these will be gone. The back of the primary also has a scallop around 1″ square that is about 1/8″ deep. I think this must have occurred during the original manufacturing (maybe when removing from the mold?) because it appears to have been ground down. I took a couple shots of this so you could see the extent of it.
I have owed the optics for around 14 years and think there is still a lot of useful life in the coatings but they are probably 20+ years old so these types of defects are perfectly normal. I really don’t think any of these cause a degradation in the views but I wanted to be sure and disclose everything I know about the optics so you are not disappointed.
Mount
So the main design points for the mount are as follows:
- Must fold up into a relatively compact space to fit in the back of my Ford Escape
- Set up/tear down time should be minimal
- Hexapod for collimation
- Full GOTO with motorized focuser and field rotator (the latter probably a future project)
- No visible wires and motors as much as possible – I really dislike everything being exposed
- Furniture quality finish
- Drive-to to avoid complex clutches etc. so slewing rate needs to be decent
Right now I’m thinking I would make the base unit and LTA one inseparable unit, with an altitude stepper driving a large diameter gear built using a long GT2 belt glued to a 1/4″ plywood “gear” that’s slightly larger than the altitude bearing so it can engage the motor below the altitude bearing. Altitude axis 3/4″ plywood with standard laminate on teflon bearings. Azimuth axis would be a lazy susan bearing (already got one) that sits on a fixed disk with GT2 belt glued to it – the azimuth motor would stick through the upper base box and engage the gear from above so all motors and electronics would rotate around the lower base box. It should be easy to hide the motors and electronics. Any cables for the UTA will go up one truss unit, including a cable to a USB 3.0 hub that connects to the Pi in the base. All functions standalone with an OnStep Controller on a Teensy 3.2 controlled by a Raspberry Pi computer built in, with it’s own wifi hub running Stellarmate and INDI drivers for all components, controllable from a tablet or PC via Wifi. The Pi will either run off the builtin wireless hub via ethernet or on my house wifi and be internet connected.
Here’s a diagram of the concept for a base and azimuth bearings:

Part of the design process is figuring out how things will work together – in the case of the base box I originally had the motor that drives the Altitude gear right in the middle under the gear until I realized no way the mirror box, which hangs down from the Altitude ring a fair bit, will clear the motor in that orientation so it got moved to the side and a 1:1 belt drive got inserted to move the motor out of the way. I suspect I’ll need to route a channel into the side of the mirror box to hide the belt and pulleys but I like the idea of nothing being outside the box!
With the mirror cell done (below) I started the structure of the telecope with the mirror box. I wanted to use a 45 degree joint so I did some research and these spline joints seem rugged enough. Stuffed with a birch insert then glued then brad nailed. The edges will be covered with birch veneer since I can never seem to cut without burning the edges! The pieces I cut out to make the 45 deg on the table saw will be gussets. The front and back will have 1/4″ birch plywood covers with a center hole and slots cut in the front for the strut attachments. I got the plastic for the covers too so ready to finish this piece off.



Mirror Cell
Using the program PLOP I’ve decided to go with a 9 point mirror cell, with three triangles. The plot of the mirror and the cell triangle layout looks like this:


In May I took the day off to get a jump on some ATM projects, including the mirror cell for my 16″. I had great fun cutting steel with an angle cutter, never done that before. Sparks!

I still have to drill holes for triangles and attachment to the mirror box, as well as for the truss attachment points. I intend to weld three 6″x1.5″ steel pieces angled along the 120deg lines and put a piece of threaded rod through the steel with nuts on either side to center it. I will then attach the heim bolts to that rod for the base of the trusses. The top attach point will also have a swivel safety clip for the top of the mirror to prevent tipping forward. I also need to drill some holes in the middle rail to hold bolts to attach a wire sling for the mirror, using 3/16″ aviation cable.
Here’s the cell assembled (ignore the red magnets and angle irons at the top)

Welding is harder than it looks 🙂 My oldest, Liam (who has had some expert instruction,) gave me a hand to get it all welded up. The frame is ready for the bolts and triangles to be added once I clean it up and paint it!
Here’s the cell welded with holes drilled (done before welding to make it easier to get it into the drill press!)

Once the mirror cell frame was welded, I punched holes on the top of three acorn nuts and threaded them onto threaded rod as pivots on which the triangles for the 9 point support system can rest. I then cut some lock nuts in half so their profile was less than the teflon sliders that will actually contact the mirror.


Next the mirror triangles were cut from some 2mm aluminum I recovered from an old computer case. The triangles rest on the acorn nuts and can adjust their angle to ensure that the mirror isn’t being distorted by the cell. I still need to cut a ring of Kydex to join the apexes of the triangles together so they don’t rotate out of position.
Finally the wire sling that will support the bottom of the mirror was fitted to one of the other bolts in the frame and left unattached for when I put the mirror in for fitting, which is after the plywood box to hold the entire assembly is complete. Thats the next step!

Current status: Mirror Cell Complete!
Upper Tube Assembly
Originally I was working on the UTA design based on Jonathan Pogson’s beautiful Merope scope – since I’m also an amateur luthier strings and tuning machines are easily obtainable from my “other” junk drawer 🙂
As I tend to I drew up the design based on the great PDF’s Jonathan posted and noodled everything out before cutting. I used a RotoZip spiral saw with an aluminum circle cutting jig. All of the aluminum parts and tools for this scope are coming from an old computer case (like really old, an old CP/M 80 S-100 system long since parted out and sold.) Since this case had a nice curve on the sides of the case I also got angle brackets from it – two of these will be the UTA connection points for the truss.


Once the rings were cleaned up I mounted the bottom brackets on the ring and test fitted with the mirror cell. This will be how the UTA sits during travel/storage.

The rings are mated with 1″ aluminum spacers, with a laminate shell inside painted black on the inside to eliminate internal reflections. I’m using camo black spray paint, which is pretty flat.

The spacers use the same star type tube inserts I will be using on the trusses for the telescope, bought on eBay for $5.09 for qty 4 . To insert the inserts, it was easiest to screw a 1/4″ screw into a piece of wood,screw the insert on, and bang it in with a hammer. Looks good!


Fridays off began this summer (I work for a school division so we bank time all year to use as Fridays off all summer) so spent a few hours in the garage working on the spider / secondary assembly for the scope. Since I had a commercial secondary mirror holder for the 3.1″ mirror I got with my primary, I just needed to make a spider and mount. The most stable type of spider has been proven to be of this design so hopefully it’ll work well once it’s in operation!

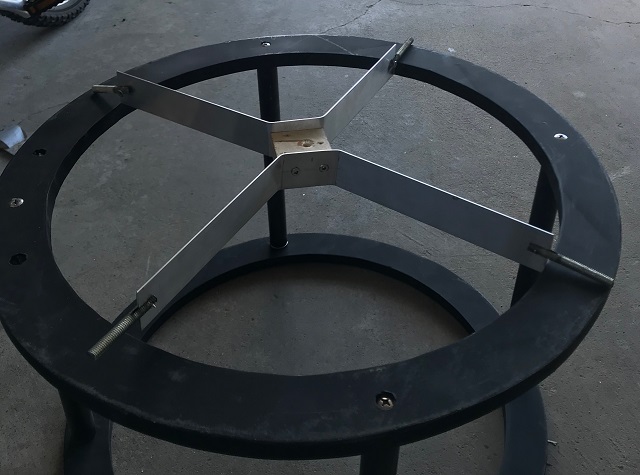
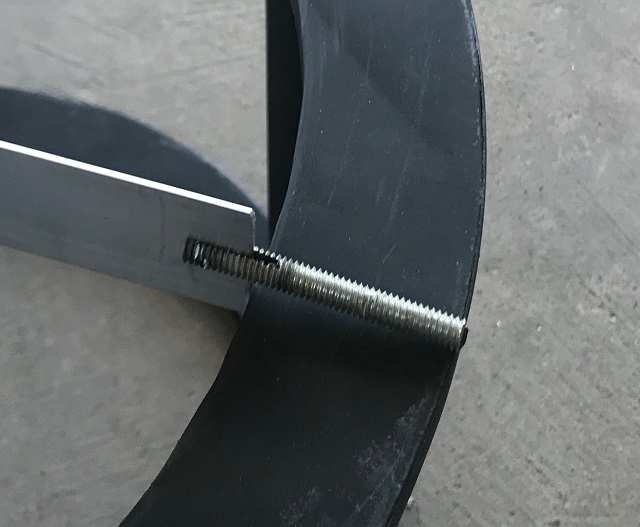



Almost ready to assemble the telescope OTA – both the UTA and LTA are complete. Unfortunately, the Heim joints for the lower end of the tube (bolts with a swivel bearing so they can adjust the angle of the truss member) are 1/4″-28tpi instead of the 1/4″-20tpi so I had to order a new tap to retap the tube inserts so rotating them will change the length of the truss (thus allowing collimation).
After testing whether I could actually get away with re-tapping the inserts (yes, it works fine) I assembled all the pieces for the OTA.



After quite a long hiatus (work, kids, blah blah blah) I’m back at it over the Xmas break – got the altitude bearings cut (as you can see I’ve gone with hemisphere’s for now to simplify the cutting) with aluminum strips since there were some uneven points in the wood.

The mirror box bearings are complete, although I’ll br replacing the rough aluminum mounts for the ring bearings with something a little more attractive. The rocker box needs to be cut right down to the minimum but I need to build the actual motor drives and see just much I can squish into the smallest space for the lowest profile. I’ll cut the box down then.


The electronics are working – I decided to put a Raspberry Pi 4 in the rocker box to control the telescope completely and use an iPad running Sky Safari as a controller rather than the Pi in the secondary cage for now, saving running any power and USB up to the secondary cage. However I’m playing with an Open Source voice control system named Mycroft that looks pretty interesting, that might be a neat addition “Mycroft, slew to the Orion Nebula please!” First things first tho!
Next I’ve glued GT2 belt material to the Altitude and Azimuth “gears” so I can attach GT2 gears to drive the telescope motions.

On the Altitude gear an axle will drive two gears, one for each Altitude gear, that are in contact with the large gear extending out from the Altitude bearing. A bushing will provide a bearing surface for the rod,

Similarly a shaft will protrude through the baseplate of the rocker box and contact the large Azimuth gear to drive the scope in Azimuth. I’ll need to work out some way to disengage both axis so the scope can be moved with the motors disengaged but to start I’ll just make the scope “drive-to” since the vast majority of the time the scope will be transported with the rocker box mated to the base and the mirror box also in place with the secondary cage mated to it.



Above is version 1 of the telescope, undriven currently, but functionally complete. Issues with this scope that will need to be fixed are:
- Too heavy. The mirror box and altitude trunnions are quite heavy to lift
- The hexapod bolts are made from 1/4″ threaded rod and bolts, which are too light for the weight they are carrying. 1/2″ would have been better (but heavier still)
However this is a great prototype and learning platform, so it’s seeing some use! Motors etc. are coming soon!